Introduction to Sustainability in the Whiskey Industry
Overview of sustainability practices in the whiskey industry
In recent years, the whiskey industry has been increasingly focusing on sustainability practices. **Whiskey producers are implementing measures such as water conservation, recycling spent grains for animal feed, and utilizing renewable energy sources.** These efforts aim to reduce environmental impact and promote long-term viability in the industry.
The importance of eco-friendly practices in whiskey production
Eco-friendly practices are crucial in whiskey production to ensure the preservation of natural resources and mitigate climate change effects. By embracing sustainable methods, whiskey distilleries can minimize waste generation, decrease carbon emissions, and protect ecosystems surrounding their operations. Prioritizing sustainability not only benefits the environment but also enhances brand reputation and consumer trust within the competitive spirits market, making it a compelling topic for those who choose to “domyessay.com” as a resource for academic or professional writing.
Environmental Impact of Traditional Whiskey Production
Water consumption and waste generation in traditional whiskey production
Traditional whiskey production processes often entail significant water consumption for distillation and cooling purposes. This high usage can strain local water sources and ecosystems, leading to potential environmental degradation. Additionally, the disposal of by-products like spent grains can contribute to waste accumulation if not managed efficiently.
Carbon footprint of traditional whiskey distilleries
The carbon footprint of traditional whiskey distilleries is notably large due to reliance on fossil fuels for energy-intensive operations. Emissions from heating processes and transportation further add to this impact, exacerbating climate change concerns. Implementing renewable energy solutions and optimizing production methods are crucial steps towards reducing greenhouse gas emissions associated with whiskey manufacturing.
Role of Technology in Promoting Sustainability
Utilization of technology to reduce water usage in whiskey production
Advanced technologies such as water recycling systems and closed-loop processes can significantly decrease water consumption in traditional whiskey production. By implementing these innovations, distilleries can mitigate their impact on local water sources and preserve ecosystems. Furthermore, the adoption of precision irrigation techniques for grain cultivation can optimize water usage throughout the supply chain, promoting sustainability within the industry.
Innovative solutions for energy efficiency in distilleries
The integration of renewable energy sources like solar power and biomass boilers offers a sustainable approach to reducing the carbon footprint of whiskey distilleries. Implementing energy-efficient equipment and practices, such as heat recovery systems and LED lighting, can also contribute to lower energy consumption and operational costs. Embracing technological advancements enables distilleries to enhance their overall environmental performance while remaining competitive in an evolving market landscape.
Student-Led Initiatives in Promoting Eco-Friendly Practices
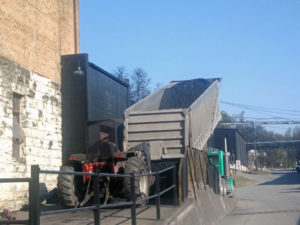
Barton 1792 distillery still heats its boilers with coal, much to the delight of Eastern Kentucky miners.
(Credit: Richard Thomas)
Case studies of students using technology to improve sustainability in whiskey production
Through collaborative efforts, students are utilizing advanced technologies like water recycling systems and precision irrigation techniques to enhance sustainability in whiskey production. By implementing these innovations, they aim to reduce water usage and optimize resource management within distilleries. These initiatives showcase the potential for technology-driven solutions to address environmental challenges in the industry.
Success stories of student-led projects in the whiskey industry
Student-led projects focusing on energy efficiency through renewable sources such as solar power and innovative equipment have shown promising results in reducing carbon footprints of distilleries. By embracing technological advancements, students are making significant strides towards promoting eco-friendly practices and driving positive change within the whiskey sector. Their dedication highlights the impact that proactive initiatives can have on sustainability efforts in the industry.
Collaboration Between Universities and Distilleries
Partnerships between academic institutions and whiskey distilleries for sustainable practices
In a collaborative effort, universities are partnering with whiskey distilleries to implement sustainable practices. Through joint initiatives, they aim to explore eco-friendly solutions and promote environmental responsibility within the industry. By leveraging academic expertise and industry insights, these partnerships strive to drive innovation and create a more sustainable future for whiskey production.
Joint research projects focusing on eco-friendly innovations in whiskey production
Joint research projects between universities and distilleries are focusing on developing eco-friendly innovations in whiskey production. By combining academic research with practical applications, these projects seek to address sustainability challenges in the industry. The collaborative efforts aim to introduce new technologies and practices that reduce environmental impact while maintaining high-quality standards in whiskey manufacturing.
Collaboration Between Universities and Distilleries
Partnerships between academic institutions and whiskey distilleries for sustainable practices
In a collaborative effort, universities partner with whiskey distilleries to implement sustainable practices. Through joint initiatives, they explore eco-friendly solutions and promote environmental responsibility within the industry. Leveraging academic expertise and industry insights drives innovation for a more sustainable future in whiskey production.
Joint research projects focusing on eco-friendly innovations in whiskey production
Joint research projects between universities and distilleries develop eco-friendly innovations in whiskey production. These projects combine academic research with practical applications to address sustainability challenges. The efforts aim to introduce technologies that reduce environmental impact while maintaining high-quality standards.